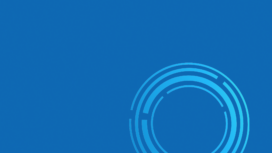
Satisfied Customers
Securing supplies and cutting transport costs thanks to comprehensive notification functions
Global groups need an efficient inbound supply chain to ensure a smooth flow of goods. The objective is for the goods to be delivered in the correct quantity, on time, correctly packaged and as economically as possible. In order to achieve this, suppliers and forwarding companies must be integrated reliably and seamlessly in the information flow of the buying company. How can external partners be integrated quickly in this process? How can the quality of notification data be improved as regards the required volume and anticipated weight of transports? How can existing packaging master data be used? An OEM has proven that with SupplyOn manual notification processes can be replaced by automated processes with a high level of quality.
Challenges
An automotive manufacturer faced several challenges in relation to its inbound supply chain: First, its transport costs were very high, due primarily to the fact that only around 65 percent of the ordered transport capacity was actually used. In addition, the products were repeatedly damaged in transit due to incorrect packaging. There were also delays in customs declaration because it was not clear which articles were in the packages and in what quantities. The transport ID, a key field for transport control, was not used systematically in the notification process. In some cases, deliveries arrived unexpectedly or too late.
On top of all that, the manual notification process was gradually being stretched to its limits in view of the growing complexity of the inbound supply chain with its some 3,000 suppliers, several million demand messages and delivery notes a year and a large number of multi-level packing instructions. The existing process was a black box: it lacked transparency and end-to-end, consistent data.
One further challenge was that management had set a target of reducing costs by a seven-digit figure.
The SupplyOn solution
To tackle the challenges in volume and transport planning, the company decided in favor of the SupplyOn collaboration platform as part of a proof of concept. The tool enables external partners to be technically integrated very quickly as well as for all the requirements and packaging information to be made available. In addition, the tool documents every notification correctly and transparently on the basis of the predecessor documents.
For weights and volumes to be calculated correctly, the applicable packaging is specified in the requirements message on the basis of the company-specific master data model. It can then be included correctly in the subsequent notification. As a result, weights and volumes can be calculated correctly at the “handling unit” and “transport” level and made available for planning purposes.
The functionality is completed by the option of printing material tags, consignment lists and delivery notes directly via SupplyOn in accordance with the Galia standard.
Project details
In the first phase of the project, the company-specific process requirements were recorded and the master data model and interfaces analyzed. A gap analysis was conducted to document the status quo and target status and to define which of the required functionalities were to be included in the proof of concept on the basis of which measurement criteria. They included the criteria for successful volume and transport planning.
At the same time, a conversion tool was programmed to generate EDIFACT requirement messages from data in CSV format and to report back the notification results converted from the EDIFACT format to the CSV target format.
The second phase of the project was dedicated to the rollout of suppliers. It was proven for the three defined proof of concept suppliers that SupplyOn carries out registration and training of suppliers very efficiently, with the result that suppliers are able in a very short space of time to receive messages and process them correctly.
The solution from SupplyOn and also the support in integration and training met with great acceptance at all three suppliers.
The manufacturer was able to prove that the notification portal implemented by SupplyOn cuts costs and significantly improves the quality of the notification data (the right quantity and correct weight and volume).
Benefits at a glance
- Potential savings in the seven-digit euro range thanks to a reduction in administrative activities and transport costs.
- Cost savings by increasing the average capacity utilization of trucks from 65 to 80 percent.
- Avoidance of impending production stops by means of reliable transport planning (collection and delivery on the notified date).
- Lower operating costs due to uniform interfaces to more than 1,000 suppliers.
- Greater customer satisfaction as a result of better delivery performance.
- Less tied-up capital thanks to a reduction in inventories, yet a high ability to deliver.
- More scope to tackle strategic tasks by eliminating manual activities.
You would like to get more information on Supply Chain Collaboration?
Just enter your contact details and we will get in touch with you as soon as possible.