How to better cope with demand volatility
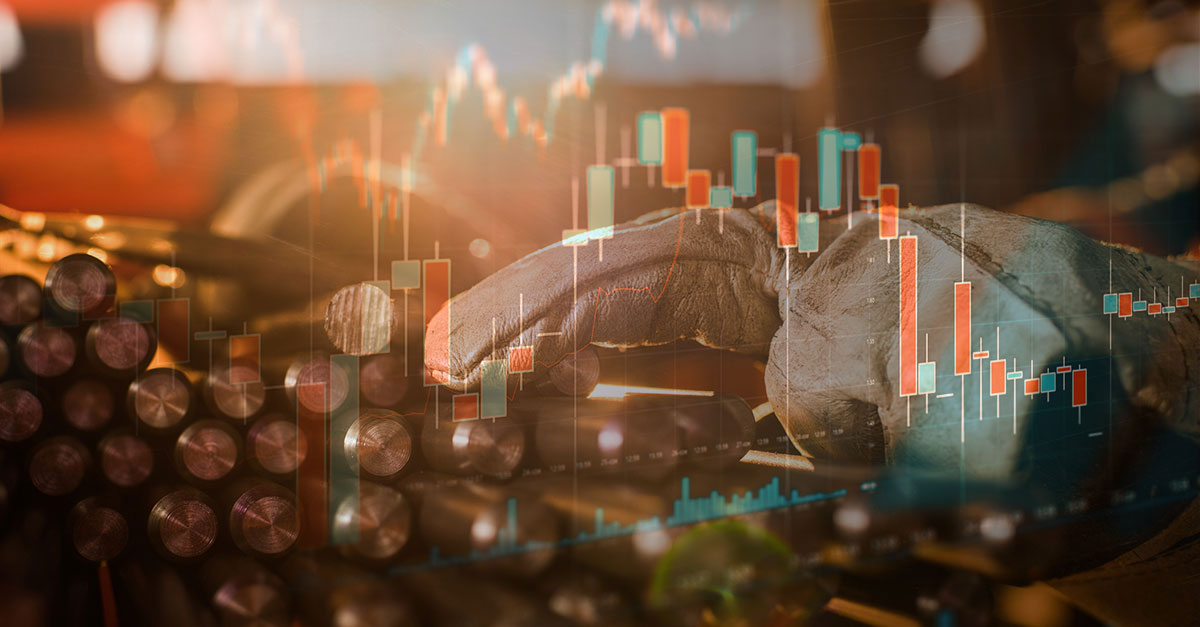
The coronavirus crisis has revealed a long-standing challenge for suppliers even more clearly: How reliable are the demand forecasts they receive from their customers? High volatility and uncertainties in demand forecasting are not limited to pandemic times. Even in the “normal state”, the originally reported requirements can differ considerably from the materials actually called off. The decisive question is therefore: How can you improve forecasting and thus also achieve a higher level of planning accuracy?
Frequent, serious forecast fluctuations put suppliers out of sync
In an ideal world, a purchasing company sends a very stable demand signal to its suppliers for the next 12 to 18 months. The weekly or monthly updates of this forecast do not indicate any major, unexpected fluctuations. Moreover, the forecasts are also consistent with the quantities ordered and delivered in the end. This means that the supplier can always plan reliably—from material procurement through production to the actual work shifts, as delivery dates draw closer.
The reality, however, usually looks quite different. Within the 12 to 18 months of a forecast period, adjustments and corrections to the demand forecasts are common. This is usually not a problem as long as the deviations are not too fundamental or too short-term. A few weeks ahead of the actual production, in the so-called “firm horizon”, things should not change too much anymore, however.
Procurement of raw materials usually requires a lot of lead time. Thus, short-term changes such as “please deliver two weeks earlier, but in lesser quantities” or “we need the materials one week later, but in double the quantity” present the supplier with major, sometimes insurmountable challenges. Quite often, the fluctuation margins depicted in the forecast are not adhered to in practice. As a consequence, high demand volatility can lead to delivery disruptions, especially reported just before the call-off.
Abrupt economic swings do often not reflect in the forecasts
To complicate matters during the pandemic, suppliers were sometimes faced with a system-imminent inertia. In some cases, ERP processes ran completely automatically, i.e. not dynamically adapted to the new situation. Forecasts may have still been based on a sales plan that was created several months or quarters ago.
Particularly in the event of rapid economic upheavals, suppliers can then no longer rely on the submitted demands. Although the forecasts are later usually corrected, this often happens very shortly before the call-off or even just before the actual delivery date. It is not just that the updated demands then differ considerably from the forecast just one week earlier. Also, these corrections often bypass the ERP system. In many cases, email, phone and fax serve as the emergency line.
However, suppliers plan their material procurement and other internal production steps well in advance—based on the reported ERP figures.
Of course, contracts include provisions regarding the quantities of purchases in the short-term horizon. However, upward adjustments of quantities during this period may pose serious challenges for the security of supply. These therefore need to be recognized or avoided.
Achieving a more reliable planning with the help of data science
But how can suppliers improve their planning reliability and meet the demand of their customers despite all the volatility? To address this issue, SupplyOn has developed a solution based on machine learning. It analyzes demand processes such as past forecasts, delivery call-offs and customer orders and then uses this information to derive predictions for the future.
Using various dimensions, it examines the consistency of demand: Do deviations occur primarily among individual customers? Or do these affect just certain plants? Do these mainly concern specific materials or material groups, or do they occur across-the-board?
On this basis, the customer’s forecast is enriched with additional information for the buyers and material planners at the suppliers’ side. Suppliers thus achieve a significantly higher level of transparency beyond the bare ERP figures. This allows suppliers to anticipate whether they can expect only minimal deviations or should prepare for considerable discrepancies in actual demand. All this helps them to validate their own planning, incorporating appropriate buffers, stock levels, order deadlines, etc.
Smooth supply chains despite high demand volatility
In brief, suppliers benefit from:
- Identifying demand patterns and fluctuation bandwidths
- Improving planning reliability by enriching forecasts with historical data and trend analyses at customer, plant and material level
- Avoiding short-term rescheduling and adjustments in production
- Preventing laborious or expensive ad-hoc material orders
- Eliminating supply disruptions to the customer
- Optimizing stock management
- Increasing customer satisfaction and loyalty, since the supplier is able to quickly respond to to changes in demand, even at short notice
- Understanding the cause of fluctuations in-depth (why, when and where these usually occur). This allows for designing targeted prevention and mitigation measures jointly with their customers
Ultimately, this benefits all supply chain participants, from the purchasing company all the way to the sub-supplier. After all, there will be fewer disruptions and, as a result, the supply chain will be generally smoother.
A valuable tool, also in times of crisis
The solution proves its worth not only in “normal times”. Suppliers benefit from its capabilities also in exceptional situations such as the current coronavirus crisis. Especially during production ramp-up it proves to be a good planning and management tool.
On the one hand, you can compare how demand evolved over the last 12-18 with current data. This can help, for example, to refine the forecast quality on the basis of typical seasonal fluctuations. On the other hand, you can also see how demand is rising again on a daily or weekly basis. This trend information, too, is extremely valuable in production and procurement planning.
Last but not least: You no longer pass on uncertainties about the current order and demand situation further down the supply chain. Instead, you can achieve some state of predictability and robustness even in uncertain times. This in turn benefits the supply chain as a whole. The so-called “new normal” of a VUCA world (VUCA = volatility, uncertainty, complexity, ambuigity) thus becomes a bit more manageable.