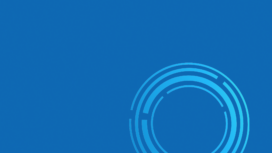
Satisfied Customers
Successful implementation of end-to-end SCM processes throughout multiple levels of the supply chain at Premium AEROTEC
Mid-2012 Premium AEROTEC GmbH (PAG) was faced with the challenge of replacing within just a few months the eSupply system used so far with suppliers, with a sustainable solution. The company opted for SupplyOn’s AirSupply solution. In future this strategic tool will handle highly collaborative order and delivery processes with suppliers as well as with PAG’s customers.
“Standard processes mean less work, reduced costs and an increase in project speed. And everyone involved can benefit from this at the end.“
“It was important for us to introduce a system that fully maps the standard specific processes of the aerospace industry,” comments Mattias Schmidt, project manager in charge of the implementation of AirSupply. AirSupply was first implemented at the three sites in Northern Germany – Bremen, Varel and Nordenham – as they are all equipped with a common central SAP system.
First, around 100 of the total 250 production material suppliers were connected to the new solution. The main advantage was that 90 percent of these companies were already using AirSupply. “These suppliers were thrilled that they would now be able to work with us via one single system,” explains Mattias Schmidt. “And for us this meant that the rollout with these suppliers was particularly easy. From a technical perspective, they were already connected and familiar with the solution. We preached to the converted!” In some cases suppliers were handling a higher order volume with Premium AEROTEC than with other customers. Therefore, an integration project for suppliers was suddenly worthwhile so everyone involved could benefit from the solution.
Implementation within just 6 months
The project to introduce AirSupply in order to handle processes with suppliers started in September 2012 and was completed successfully both “in time” and “in budget” in March 2013. The project was divided into three areas which ran in parallel:
- Technology / IT
- Processes
- Supplier Management
The Technology / IT stream involved making the necessary adjustments in the internal ERP system. Seeburger, another IT service provider involved, was commissioned with setting up the middleware between the ERP system and SupplyOn and dealing with the mapping. Finally, SupplyOn configured the solution according to the customer’s requirements and tested it together with PAG. Although the tests were extensive and partly very complex – the test cases had to be carried out as an end-to-end process – they went smoothly and according to schedule.
Professional support
The Processes stream whose aim was to define, document and validate the processes was carried out by Premium AEROTEC employees with the help of SupplyOn Consulting.
As part of the Supplier Management stream SupplyOn Consulting arranged for suppliers to receive training and information regarding the technical and contractual aspect of data exchange via AirSupply.
“SupplyOn’s Consulting team was very professional and worked in a structured way according to tried-and-tested standards. This made it very easy for me to manage the project in-house. And although no one at PAG believed at first that the project could be completed in such a short time, we easily met the deadline,” sums up Mattias Schmidt.
End-to-end SCM processes from OEM to tier 2
PAG started using the solution with its customers in April 2013 when the first part numbers were ordered via AirSupply. An end-to-end mapping of the supply chain is now possible – a customer order triggers a secondary demand which is sent automatically via AirSupply to the sub-supplier of Premium AEROTEC.
The next step will be the connection of the Augsburg site to AirSupply. This will take place as soon as Augsburg’s current system, which is highly fragmented and complex, has been harmonized and transferred to a central ERP system. This will be followed by the connection of further suppliers – the long-term goal is to integrate all 250 product material suppliers – and the replacement of all paper processes.
About Premium AEROTEC
Premium AEROTEC GmbH is one of the world’s leading suppliers in the aerospace industry, specialized in design and production of large and complex components. The company’s core business includes the development and manufacturing of aircraft structures made of metal and carbon fiber compounds as well as equipment and manufacturing systems. Premium AEROTEC employs over 8,000 members of staff and generated sales revenues of 1.5 billion euros in 2012, with production sites in Augsburg, Bremen, Nordenham and Varel as well as in Brasov, Romania.
Further customer statements and case studies on AirSupply
You would like to get more information on AirSupply?
Just enter your contact details and we will get in touch with you as soon as possible.