Product development: the why & how of supplier-initiated change requests
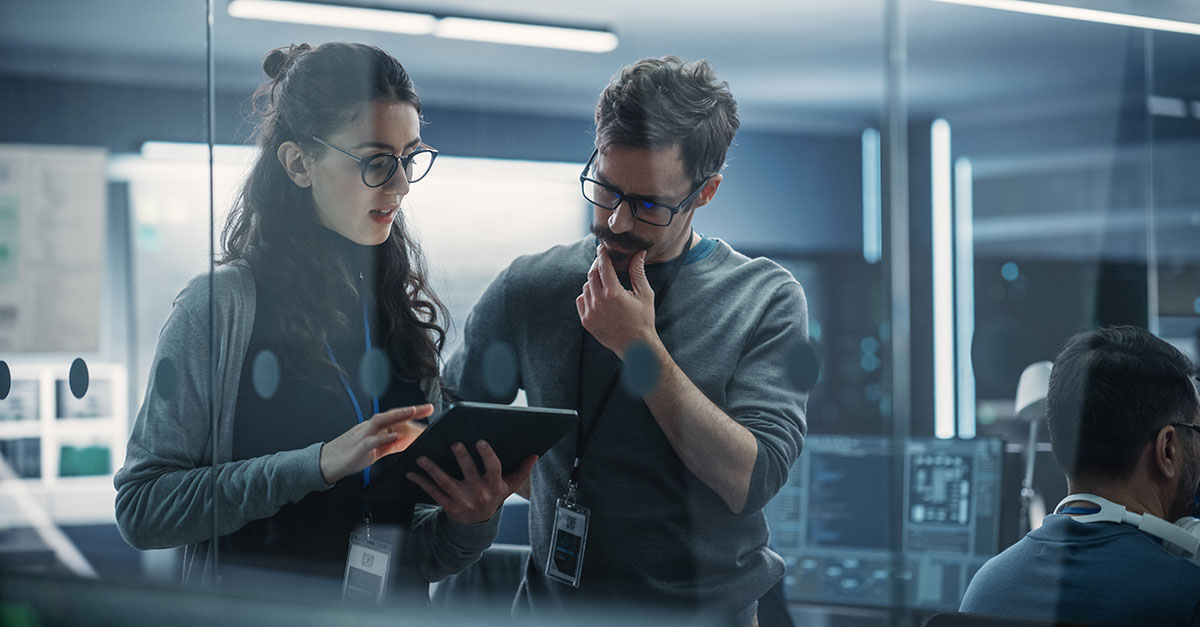
Feasibility studies play a crucial role in the automotive industry during the procurement process for parts under development. After all, even before these new parts are developed and contracted, companies need to ensure that they can be delivered in the required quality and quantity, on time and at appropriate conditions. SupplyOn Technical Review has been efficiently handling all of this for years. In most cases, the customer provides the specifications. But it can lead to even greater efficiency and project success if the suppliers can also initiate changes themselves.
The classic Technical Review process
Technical verification is the process of verifying the quality, quantity, delivery dates, and conditions of a new part. For this purpose, the customer company requests information from the suppliers by means of a questionnaire. The customer then assesses the supplier’s feasibility and maturity.

Change management: a new process for Technical Review
Automotive supplier ZF Friedrichshafen has been one of the main users of the Technical Review process since its inception. And because Technical Review has worked so well from the start, they wanted to see if Technical Review could be extended beyond the standard process.
ZF project manager Alejandra Rangel Granados explains: “We often have a situation where a supplier needs to independently coordinate and approve necessary or desired changes to the product and process with us as the customer before the change is implemented. In this way, the supplier can be sure that ZF, as the customer, agrees to the change. “
And it was no coincidence that SupplyOn already had a concept up its sleeve. There were already concepts on how Technical Reviews could also be initiated by the supplier. With a small expansion of the Technical Review, the time had come at the beginning of 2023: the improved process based on Technical Review was ready for ZF.
How the supplier-driven Technical Review process for change requests works
As a prerequisite for the supplier-driven process, the customer first creates a template. This template defines the type of changes, such as product information, that the supplier can send to the customer.
The supplier can then use this template to send structured change requests and start the coordination process with the customer. After receiving the request, the customer may need to coordinate further details with the supplier and check the feasibility of the change. The result is immediately displayed to the supplier in Technical Review and sent as an email notification.

Advantages of the optimized process
ZF project manager Alejandra Rangel Granados: “The ZF Commercial Vehicle Solutions division has been using the new process with its suppliers since mid-January 2023. Previously, change requests for parts and processes were made via unstructured e-mail communication, which was difficult to track. Thanks to SupplyOn, we can now offer a fully electronic, easily traceable and data-secure process. In addition, we are now much better informed before the supplier makes any changes.”
Suppliers also benefit from the new process. They now receive timely feedback on important change requests. Emails from the supplier are no longer lost because the change is stored transparently and securely at SupplyOn.
Meanwhile, SupplyOn is already making plans for the next expansion stages of Technical Review. Product Manager Martin Weber comments: “We are sure that we will be able to implement further use cases based on Technical Review quickly and easily.” So, it remains to be seen what the future holds for the all-rounder Technical Review — in any case, the end of the line does not seem to have been reached yet.