Interview: “Supply chain connectivity gains traction”
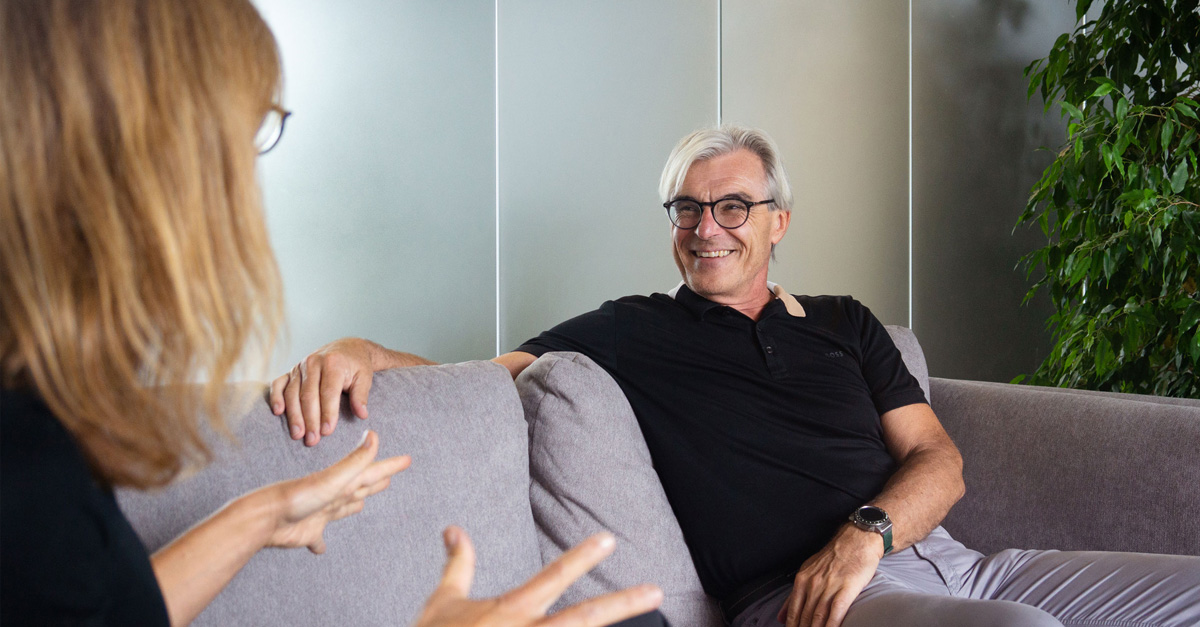
Christian, you have been involved in numerous working groups on the subject of “industry connectivity” for some time now. What topics are currently being discussed and what trends are emerging that automotive suppliers will have to be prepared for?
Essentially, the following four topics are driving the industry at the moment:
- increasing product quality
- higher transparency with regards to the capacity of suppliers — both in the long term and in the medium and short terms
- ensuring the traceability of the parts and components that have been assembled
- increasing sustainability at all levels
As a mega-trend, it can be noted that in all these processes, the volume, timeliness and granularity of data is playing an increasingly important role.
The first two topics mentioned — improved quality and more transparency in capacities — are not new. Manufacturers have been calling for this information for years now. Why are these two topics currently so much in focus — and what has changed compared to the past?
That’s true, both are lived processes for which an intensive exchange of data has been established for some time. However, this is currently taking on a whole new quality. On the one hand, because today manufacturers are demanding not only more data, but also more detailed data; on the other hand, because the exchange of data is being extended across several delivery levels. Another new aspect is that data must increasingly be supplied electronically.
Up to now, quality data has mainly been exchanged on paper. Or it remained with the supplier as long as there were no quality issues. Now the data is to be transferred electronically and, in the best case, derived directly from the production process.
Today, capacity data is very much about early detection and avoidance of potential bottleneck situations. After all, everyone is familiar with the current discussion about supply chain problems. In this context, manufacturers are demanding insights over a much longer time horizon than in the past; in many cases, periods of up to 36 months need to be covered. In addition, and especially in the short term, a much higher frequency is required. Updates at daily intervals are no longer the exception. Here, too, the trend is emerging that data must be delivered automatically via an interface. There is no other way to manage this. For suppliers, this means that they must be able to operate this interface and that their internal systems, such as the planning software in use, can be docked onto this interface.
The issue of traceability is not really new either. What has changed here compared to the past?
Thanks to various Industry 4.0 initiatives such as GAIA-X, it is now easier to provide consistent data from serialized production. In the past, this was possible at this level of granularity, but it was extremely time-consuming. Manufacturers are calling for this data to a greater extent, of course, in order to be able to act as quickly as possible in the event of a recall, but above all as targeted as possible, thereby avoiding greater financial damage.
Targeted traceability is also essential in order to be able to clearly identify and limit the affected components and vehicles. This ensures that only vehicles that are actually impacted are recalled. The costs of recall campaigns can quickly run into millions. With every vehicle that does not have to be taken to the repair shop unnecessarily, the financial damage can be limited. But it is even more important to prevent possible damage to life and limb.
The fourth topic you mentioned was sustainability. That’ s really on everyone’s lips. So, what do you see coming for suppliers in concrete terms?
The EU has just issued a regulation that requires a Corporate Sustainability Reporting for all companies with sales of more than EUR 40 million from 2024 onwards, with retroactive effect from 2023. This means that companies should already adapt to it now and make the necessary preparations. Four years later, i.e. from 2028, this reporting will then be mandatory for all companies within the EU, including smaller companies.
The seriousness with which the EU is pushing this issue should not be underestimated. The Corporate Sustainability Reporting has a similar status to tax declarations. In other words, the data it contains must be verified, certified and approved by an independent authority. Some of this data is already exchanged via SupplyOn and is therefore already available in a structured form. We will continue to expand this offering. Overall, we have been looking at how we can support our customers in providing the necessary data for environmental protection and sustainability for some time now and are expanding our services accordingly or offering new ones.
You mentioned interfaces earlier, through which this data will have to run in the future, because otherwise the flood of data cannot be managed. What do suppliers actually need to do here? Are there pragmatic approaches that can be implemented with little effort via plug-and-play? For smaller suppliers in particular, these challenges are hardly manageable otherwise.
Yes, connectivity plays a major role in all these topics. The importance of connectivity is also shown by a recent study by IDC on networking in the German industry, which shows that only 23% of the economy is at a “high” level of networking and therefore concludes that German companies have a lot of catching up to do here.
But here comes the good news: Yes, there are connectors that allow suppliers to easily and cost-effectively hook up with their business partners. SupplyOn has developed a solution that optimally supports companies of all sizes in the complex field of integration. It enables internal ERP, MES, quality or other systems to be connected to the SupplyOn platform in a short time. Since many important industrial players around the world are already electronically linked via SupplyOn, this means that there is no longer any need for individual connections.
So, what would you advise a company to do if it wants to be well prepared for the future?
That’s a tough question, because it always depends on a company’s maturity level which next steps will bring the greatest benefits. It is certainly helpful to start with a rigorous analysis of one’s own digital capabilities and then to compare the requirements of customers and suppliers. In the next step, you should look at where you can achieve “quick wins”. This will motivate your own team to continue or convince a reserved management.
Thank you very much for the insightful talk, Christian.