Leonardo advances its supplier collaboration with AirSupply
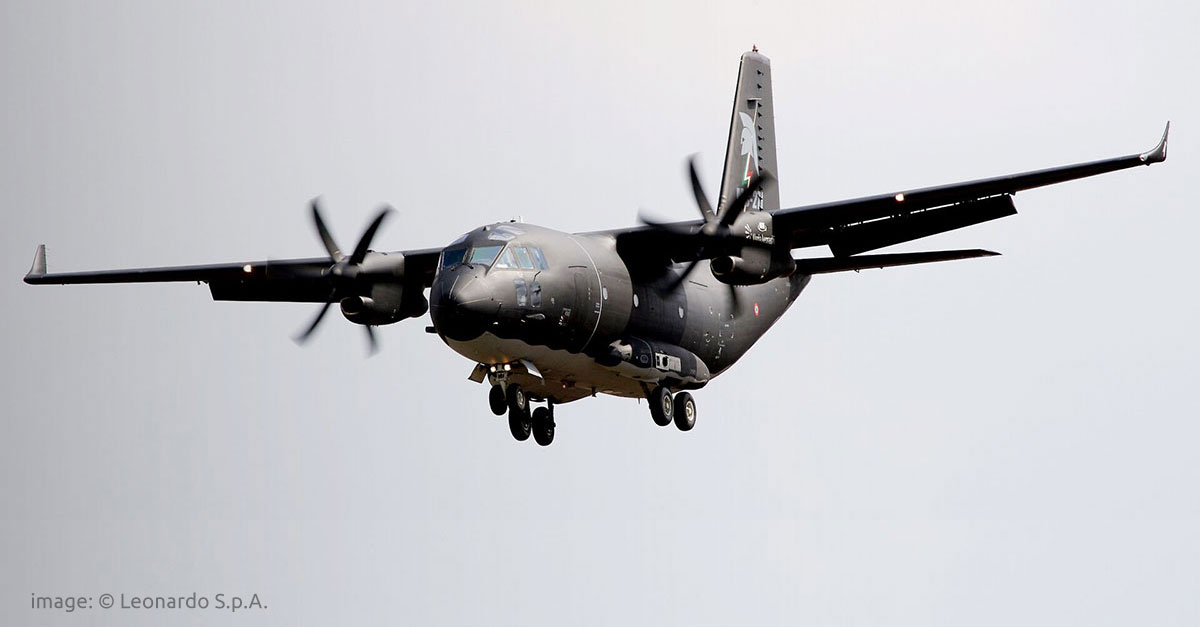
Leonardo, a major aerospace, defence and security company, wanted to harmonize and improve the digital collaboration with its suppliers throughout the group. By implementing AirSupply, Leonardo benefits group-wide from efficient electronic processes that increase transparency, traceability and responsiveness throughout its supply chain and improve inventory control.
The challenge: multiple supplier collaboration solutions in use
Back in 2016, when different aerospace companies merged to form the Leonardo Group, each of these former companies had its own way of supplier collaboration in place. Thus, the procurement processes, collaboration tools and degrees of digitization varied greatly in the new Leonardo divisions. This is why the company set out to harmonize and standardize its supplier collaboration to have one digital platform and one common procurement process within the group.
The solution: one common e-collaboration platform for all
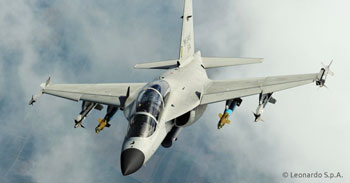
Consequently, Leonardo looked for a standardized cloud platform which was also widely used in the industry. The decision fell on AirSupply from SupplyOn, the leading aerospace supply chain platform. As Leonardo has a similar supply chain as other European aircraft manufacturers, onboarding the supplier network promised to be smoother and quicker than with other vendors.
Leonardo Global Solutions, the central corporate procurement agency for all indirect spend, piloted AirSupply first. Then the Aircraft and Aerostructures divisions for direct procurement followed suit. Both divisions had previously had a sophisticated, in-house developed supplier collaboration solution in use. Thus, buyers and suppliers of these two divisions were already accustomed to efficient digital collaboration, so the change to AirSupply proved to be smooth and easy.
Parallel to the rollout of the next division, Helicopters, Leonardo launched a massive supplier onboarding initiative and also actively engaged in further enhancements to the AirSupply solution. Due to the platform’s community setup, the modifications implemented for Leonardo ultimately benefit everyone in the AirSupply community.
The strategic importance of AirSupply and Leonardo’s commitment to the solution is underlined by the internal scope of the project: “To date, it has involved 700 buyers in ten procurement offices as well as 63 plants across Europe and the US. Seven ERP-Systems were connected for this purpose”, explains Angela Marotta, Project Manager for the Supply Chain Portal at Leonardo.
Outlook
“And we are still expanding,” she adds. After rolling out to all five Leonardo divisions, AirSupply has also been introduced to various Leonardo subsidiaries and affiliated companies.
The implementation throughout the Leonardo Group is ongoing.
Angela Marotta, Project Manager Supply Chain Portal, Leonardo Global Solutions
Currently, 900 suppliers are connected directly and another 3,000 via e-mail access. But Leonardo is working on increasing these numbers ever further. The focus here is primarily on international suppliers and EDI connections to strategic suppliers.
In addition, Leonardo is working on an even closer collaboration with its suppliers on quality issues via the SupplyOn Problem Solver. On top, Leonardo has linked the AirSupply solution to its Transportation Control Tower in order to optimize inbound and outbound transports.
Conclusion
“We are very satisfied with the platform,” summarizes Cristina Nadia Crespi, Head of Supply Chain Services at Leonardo.
AirSupply is a powerful tool for the procurement departments of the Leonardo Group. It enabled us to find a common working method. Moreover, we benefit from high traceability, reactivity and inventory control in our supply chain.
Cristina Nadia Crespi, Head of Supply Chain Services, Leonardo Global Solutions
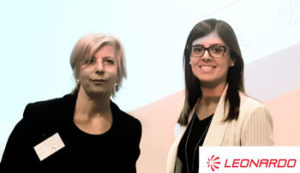
For Leonardo, the AirSupply project was the starting point of their digital transformation journey which will also include innovations in big data analytics and robotic process automation (RPA) for their procurement.
Benefits
- Efficient digital supply chain collaboration with a group-wide, common process and methodology
- Full traceability throughout the process from purchase order to despatch advice, combined with transparency of Leonardo’s relationships with its suppliers
- Enhanced responsiveness of Leonardo and its supply chain to changes in production, which proved to be highly beneficial in ensuring full business continuity and resilience during the coronavirus pandemic. Moreover, this helped Leonardo build a more open and trustful relationship with its supply chain
- Improved inventory control and reduced stock levels by blocking despatch advices that are too far ahead of their due date
- Considerable acceleration of the goods-receipt process through the wide-spread adoption of despatch advices in combination with barcode readers at the plants
Success Factors
According to Cristina Nadia Crespi, one of the key success factors of the project has been the central innovation team which has been “the driving force directly from the center of Leonardo”. Adding to that, the plants were highly committed to the project as they were eager to reap the benefits of a paperless, smooth and efficient digital process.
Secondly, the project benefitted from the fact that two divisions had already had a mature digital collaboration process in place. This significantly facilitated both the speed of implementation and the supplier onboarding.
As Angela Marotta points out, Leonardo also “invested a lot of effort in change management to pave the road for a smooth adoption”. Last but not least, Leonardo’s IT department and its responsive development team and help desk contributed considerably to the project’s success.
About Leonardo
Leonardo, a global high-technology company, is among the top ten world players in Aerospace, Defence and Security and Italy’s main industrial company. Organized into five business divisions, Leonardo has a significant industrial presence in Italy, the United Kingdom, Poland and the USA.
In 2019, Leonardo employed nearly 50,000 people, recorded consolidated revenues of €13.8 billion and invested €1.5 billion in Research and Development. The Group has been consecutively named global sustainability leader in the Aerospace & Defence sector of the Dow Jones Sustainability Index (DJSI).