A convincing industry approach: SupplyOn’s Rail Community boosts the efficiency of the railway industry
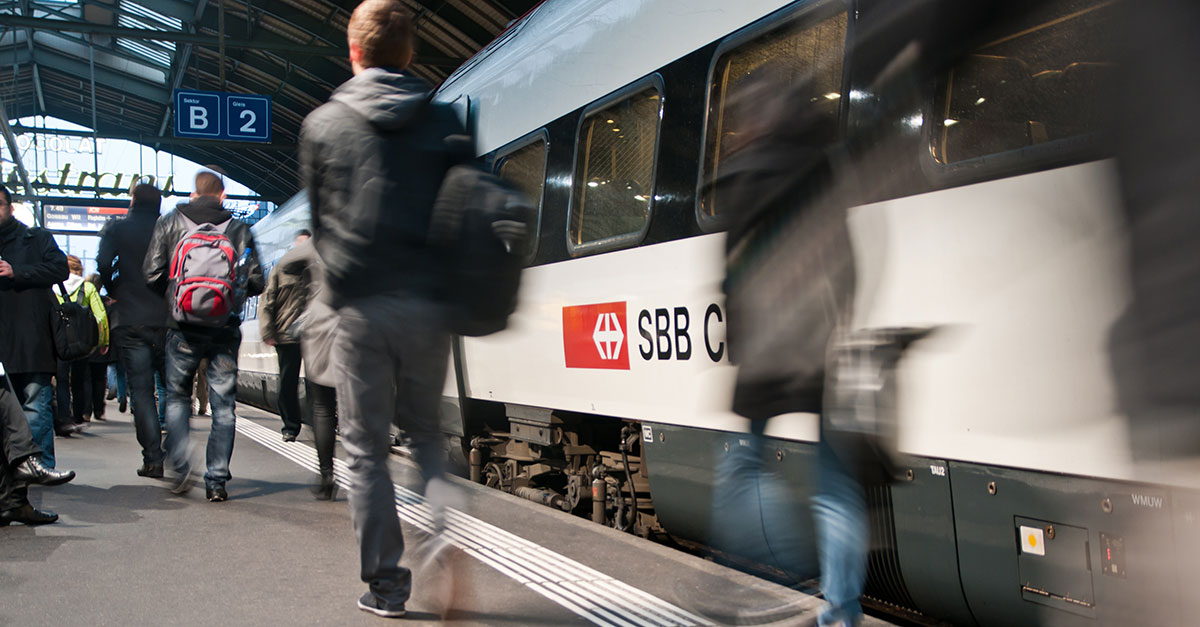
The Swiss Federal Railways (SBB), with around 34,000 employees, a transport network of over 3,000 kilometers and almost a half billion passengers per year, is the national railway company of Switzerland, consisting of the four divisions Passenger Transportation, Cargo, Infrastructure and Real Estate. In 2016, the division Passenger Transportation took the initiative to transition the ordering process, until then carried out with high manual effort by email and fax, to a continuous digital process using the RailSupply solution from SupplyOn. The goal of this changeover was to significantly streamline the SBB’s purchasing and procurement logistics.
There were two main reasons SupplyOn was selected as the platform for managing the entire process, from ordering to payment, electronically: For one, SupplyOn’s industry approach, which offers the advantage of being able to fall back on an existing network of companies in the rail supply industry. Secondly, the decision-makers at SBB also recognized SupplyOn’s flexibility for joint development of functions for the rail supply industry.
Gradual implementation at process, supplier and division level
Before rolling out SupplyOn on a grand scale, a pilot project with selected suppliers provided ample verification that the new process execution was running smoothly. During implementation, pilot and rollout, project management worked in close conjunction externally with suppliers, and internally with IT and the various purchasing areas – a significant factor in the successful organizational integration of suppliers and the technical integration of internal systems in SupplyOn.
The following implementation steps have been established on the process side:
- Order, order confirmation and Advance Shipping Notification (ASN) to form the basis of a continuous digital purchase-to-pay process
- Invoice, including automatic comparison with data from the preceding processes of ordering, order confirmation and Advance Shipping Notification (ASN)
- Demand forecast, in order to further optimize the entire process and expand planning options. This supports more accurate stock planning and a reduction in stock level on both sides of the supply chain.
In the initial step, SBB has connected 15 business partners from the Passenger Transportation Division on the supplier side. This number will gradually rise to about 350, among them suppliers of other SBB divisions as well.
It is noteworthy that the SBB also integrates business partners with whom they work only temporarily at project level. Once a specified number of call-off orders have been executed over a certain period, the supplier is integrated into the digital process in order to ensure the efficiency of the project.
Once the relationship to a supplier has taken on a certain regularity, the process can be switched to be processed electronically. It is an important objective for us to optimize all business transactions with regular data exchange in this way – even when the collaboration is clearly time limited.
Georg Spring, Head of Strategic Purchasing of Replacement Parts at SBB
SBB is also taking a step-by-step approach on a divisional level: The forerunner is the Passenger Transportation division, followed by the divisions Cargo, Infrastructure and Real Estate, which have also opted to change over to digital purchasing processes. Suppliers supplying several SBB divisions will benefit in particular.
A higher quality of collaboration
The main advantage of collaborating via the RailSupply solution from SupplyOn lies in the enhanced quality of the information exchanged between SBB and the supplier. “By mapping the data, we make sure that the supplier’s information is precisely the same as the data in our system. This has also significantly improved the quality of our collaboration. Where misunderstandings often occurred in the past, they have now been eliminated since everyone is always up-to-date”, said Spring. This not only makes order processing, invoicing and payment more reliable and faster, it also eliminates many manual (control) activities in invoice verification.
The complete implementation of demand forecast, the reduction of stock levels also becomes a focal point for optimization. The goal is to double the stock turnover rate while ensuring high security at lower stock levels, so that the necessary parts are available for production when needed.
Benefits of the RailSupply solution from SupplyOn
- Improved collaboration between SBB and its suppliers, since the high quality of data practically eliminates misunderstandings
- Reliable and fast purchase-to-pay process (order process – from the order to the Advance Shipping Notification (ASN) to the invoice)
- Standardized and simplified process for order confirmation
- Improved security of supply, and more efficient goods receipt process
- Reduction of time and effort in invoice verification thanks to the high quality of incoming invoices
- Reduction in stock levels via implementation of demand forecast
Outlook
SBB is advancing its comprehensive digitization strategy while at the same time consistently rolling out the RailSupply solution and continuously expanding its use. The goal of this strategy is to further optimize supply-chain processes. The initial experience with SupplyOn has sparked an appetite for more: SBB and SupplyOn are jointly working on the continuous expansion of digitization to include additional order types and vendor-managed inventory, as well as optimization of supply and delivery processes.
By the way: At InnoTrans 2018, SBB was named “RailSupply Champion 2018” for this excellent project.