5 Common invoicing problems and how to solve them
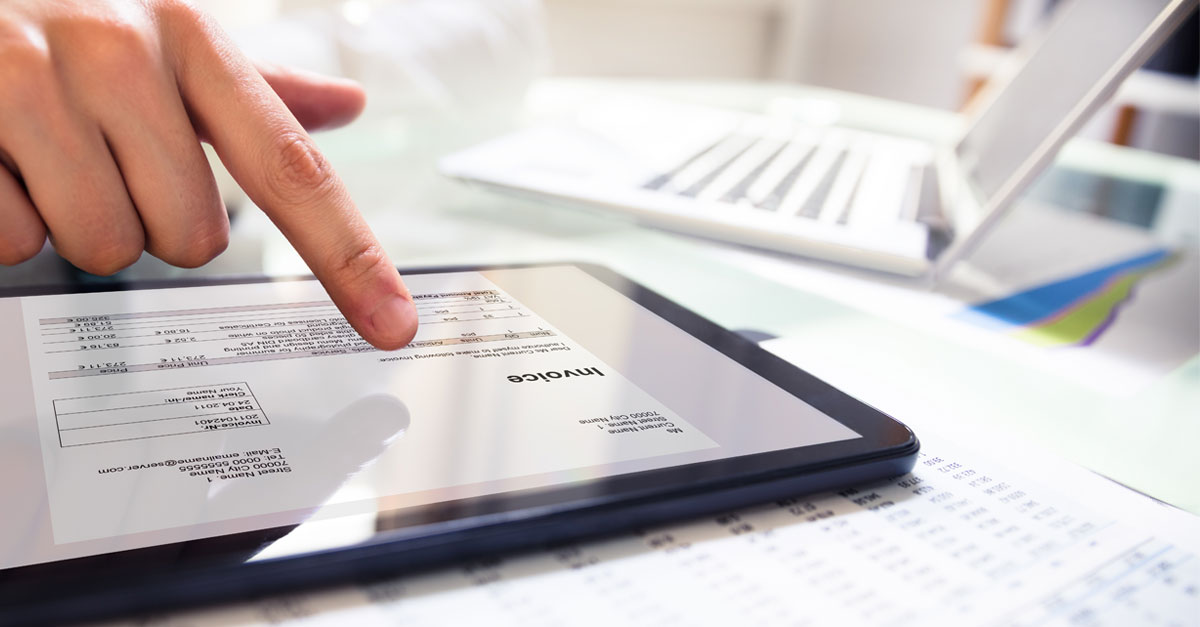
If you believe what you read in the headlines, we’ve already arrived in the brave new digital world. But when it comes to the subject of invoicing at least, the world is currently far less digital and “brave” than it could be. What’s the problem? What problems do companies face in the invoicing process? And how can these be solved?
These are precisely the questions we’re going to get to the bottom of here.
In essence, there are five main problems which in turn lead to booking difficulties, unnecessary additional work, longer processing times and excessive costs:
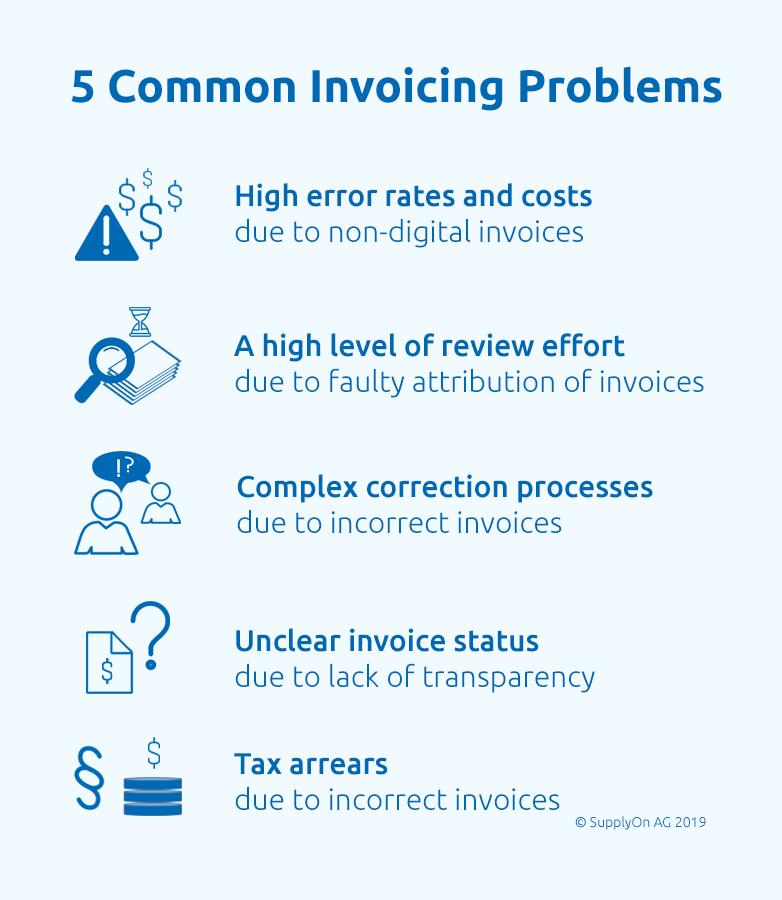
Let’s have a closer look at them:
Problem 1: High error rates and costs due to non-digital invoices
According to the current Billentis Report, 55 billion invoices are already being sent out worldwide in paperless form. But that’s only a meager 10 percent of the total. For processing purposes, this means that the remaining 90 percent require manual entry – or else the invoices have to be digitized by means of scanning.
All of this incurs considerable additional expense for the recipient and results in errors. Don’t forget: scanning solutions can be error-prone, too. The invoice to be digitized may be difficult to read, for example. Information may be incorrectly attributed. And even the most perfectly scanned invoice is useless if the paper original was faulty or incomplete.
Solution:
The only solution is to create and send the invoice digitally. This avoids media breaks and incorrect entries during digitization. Last but not least, it saves a lot of time, resources and costs. According to Billentis, the savings potential is just under 60 percent per invoice. For example, invoices sent via the SupplyOn platform contain only verified and structured invoice data that can be transferred directly to the recipient’s ERP system for immediate further processing.
Problem 2: A high level of review effort due to faulty attribution of invoices
A digital invoice alone is not the solution. Invoices often cannot be clearly attributed to the corresponding orders. The reasons for this can be many and varied: suppliers and purchasing companies may have an “invoice universe” of their own, using different descriptions and special invoice or article numbers. Sometimes the corresponding information is missing altogether. The supplier might combine several orders in a single invoice – or only issue a partial invoice for a larger order.
Changes in price or quantity may have occurred during the ordering process that have not been correctly entered in the supplier’s or recipient’s invoice system. Or else a different quantity was delivered than originally agreed, or in different denominations. A complaint may have since been lodged. Or the buyer might have partially cancelled the order.
In some cases, government regulations on invoicing barely provide any information about the order as in China with its Fapiao (Golden Tax System).
Solution:
As a result, efficient invoice processing requires a focus that goes beyond the area of invoice receipt to payment. It is crucial to address the entire process – from order to payment (Purchase-to-Pay or P2P) – in a single digital system. An integrated P2P process automatically compares order data, advance shipment notice, goods receipt and invoice data. Faulty invoices are immediately identified and automatically rejected.
Even greater efficiency gains can be achieved if this check is carried out in advance, i.e. before the actual invoice is issued. With SupplyOn, for example, companies can only invoice previously validated data. This allows for an automated accounting rate of almost 100 percent, reducing administrative effort for invoice verification to virtually zero.
In addition, it significantly reduces processing times. Payments can thus be made in good time, avoiding dunning charges and allowing more widespread use of discounts.
Problem 3: Complex correction processes due to incorrect invoices
Over and over again there are erroneous invoices. In addition to the examples mentioned above (changed quantities or prices, missing or incorrect information, complaints, cancellations, etc.), there are other sources of error. Perhaps the negotiated invoice amount was exceeded. Or the rigorous legal requirements that apply in particular countries – such as the Chinese Golden Tax System – were not adhered to.
On top of this: the more manual the method of invoice processing used by the supplier, the greater the number of errors. Similarly, the common practice in China whereby the customer and supplier agree on the correct invoice content and scope by telephone often leads to misunderstandings.
All this often results in very complex and time-consuming correction processes, which sometimes even span several loops.
Solution:
An automatic check of all invoice data before the invoice is actually issued is the be-all and end-all. In addition to order data, advance shipment notice and goods receipt, further details have to be included. This includes customer specifications for the accepted invoice scope or invoice format, for example, as well as the legal requirements of the respective countries. Any ambiguities or requests for changes can then be resolved quickly, easily and transparently – completely digitally in the course of processing via SupplyOn.
Problem 4: Unclear invoice status due to lack of transparency
Often the current status during invoice processing is not clear: has the invoice been received? Has it been checked? Is it correct? When will it be posted, when will it be paid? The status of all these individual stages and the time frame involved often lacks transparency – not only for the supplier but for the customer too.
As a result, more and more inquiries arise, especially in the case of long processing times. Answering these questions further burdens the accounting department and delays the process.
Solution:
An invoice solution is needed that makes the current invoice status transparent to all parties, indicating potential errors and corrective measures. Even better: it should not just display errors and corrective actions, but also automatically notify the invoicing party. The advantages are obvious: a high level of transparency, less effort, faster and more efficient processes.
Problem 5: Tax arrears due to incorrect invoices
If the invoice doesn’t meet VAT requirements, things quickly get very expensive. It’s not uncommon for an invoice not to meet such requirements – especially when the tax requirements of the sender and recipient countries have to be complied with in cross-border supply relationships.
If an incorrect tax invoice is not recognized and the input tax is incorrectly deducted, there is a risk of an additional subsequent payment being due. This not only costs money, it also generates extra internal expenditure.
Solution:
Here, too, a system-supported, digital preliminary check of all invoice data pays off in the truest sense of the word. This is because a so-called compliance check is also carried out. This involves a check as to whether all the information required for a tax-compliant invoice is included. SupplyOn even takes into account the current tax and legal requirements of over 40 countries worldwide.
Conclusion
Many invoicing processes are still far from efficient. They needlessly create much more time, effort and money. But all this can be changed. The prerequisite is a completely digital process. It is important for the data not only to arrive “in some kind of digital form” (e.g. by e-mail or PDF): it has to be structured too. Only then can it be processed electronically without a hitch.
Above all, however, the entire process has to be taken into account. And this starts with the order. SupplyOn therefore continuously updates and enriches order data during order processing. It is crucial for the information from the preceding documents, shipping notifications and goods receipts, to also be included. After all, it is only together that they form the correct data basis for the invoice. Further sources of error can be eliminated by automatically pre-attributing the corresponding invoice fields based on this data.
All this ensures the correct purchase order reference, enables the invoice to be clearly attributed and accelerates processing, clearance and payment.
And if an automated compliance check is also integrated before the invoice is sent, the main sources of error are taken care of. This validation step ensures that the electronic invoice is not only correct in terms of content but also formally and in terms of tax law.
At this stage we really can say: welcome to the brave (new) digital world.