InSight, InControl: Real-time position and quality monitoring for production material transports
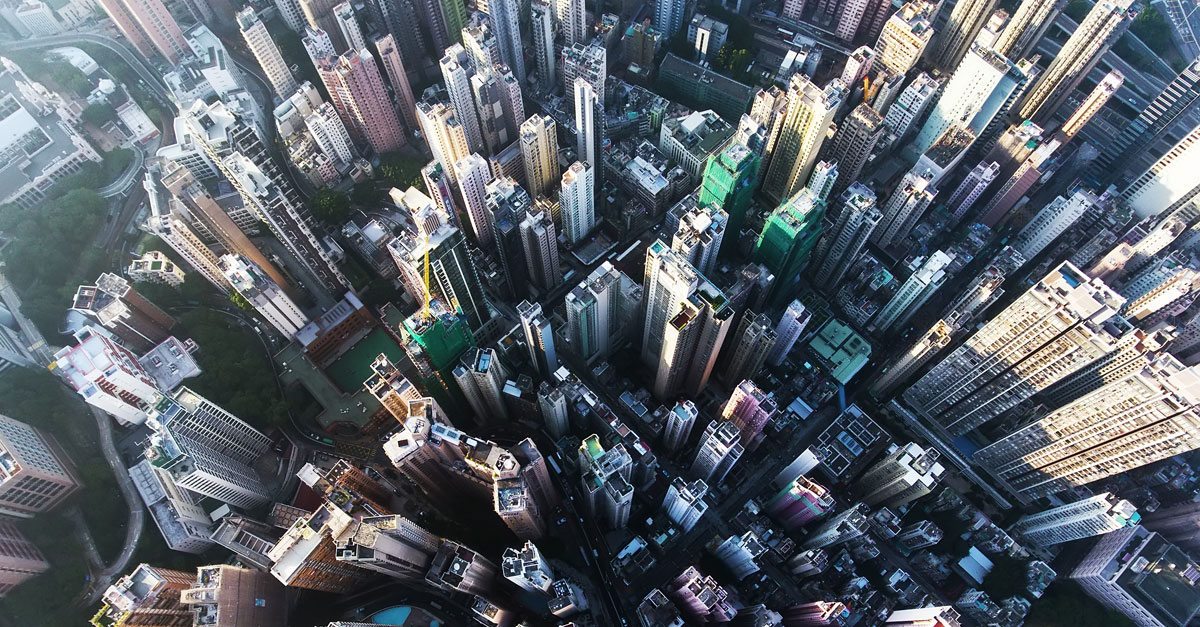
A materials controller needs up-to-date information at all times for production planning purposes. He needs to know whether the goods required are going to arrive at the plant in time – and whether they will do so in an intact state, a very important point when it comes to sensitive components. And all this preferably in real time, of course. But this is a lot more than what most track-and-trace solutions have to offer.
“Material, where are you?”
The latter are generally only able to tell you where a truck or a container is located at any given time. Whether the urgently required materials really are inside the truck or container – that’s at best a matter of conjecture or hope.
Sea freight is one big black hole: while a container is at sea, the materials planner generally has to spend weeks trusting blindly that it will arrive at the port on schedule. Delays are common at sea, however – due to the weather, altered schedules or slower travel speeds to save on fuel costs.
In order to ensure that there are no unpleasant surprises at the port or later at the plant, a solution is required that is capable of one thing above all else: real-time visibility. And it has to apply concretely at the material level.
Seamless tracking on land and sea
The data required for this is generally available but saved separately in dedicated systems. At best, the supplier will have information in his ERP about which material is in which container, for example. But generally speaking, not even the shipping agent transporting the production material to the nearest port has this information.
This is because it’s not until the goods arrive at the port that they are loaded into a container – usually by a different logistics service provider, the so-called consolidation center operator. The latter then types the details from the paper-based freight documents into his Transport Management System (TMS) so as to be able to submit the advance customs declaration, for example. As a result, the data is located in separate silos and there is very little exchange, if at all. This is even more true if the transport is intermodal, i.e. where land, air and sea freight are combined.
Here, SupplyOn is able to offer Real-Time Visibility – a component of Visibility & Analytics: it’s a solution that eliminates precisely this separation of data so as to allow seamless tracking of the material across all transport modes by means of a so-called pairing system. Pairing means establishing a connection between material and transport based on a unique auto-ID (label, sensor, RFID). During the trip, the ETA (estimated time of arrival) is continuously analyzed and an ETA update is sent out if delays are likely.
The focus is not just on time but on quality, too
This data is crucial for the material planner to be able to act flexibly and adapt production planning to potential changes early on. While this information is valuable, it is often only one side of the coin. After all, it doesn’t reveal whether the material will actually arrive intact and can therefore be used in production as planned. This is especially critical in the case of sensitive components and materials such as heat-sensitive adhesives, sensitive carbon fiber parts or metal parts that are susceptible to corrosion.
Here’s an example: an adhesive arrives by ship at the port of Marseilles in the south of France. Due to a strike, however, customs clearance and unloading of the container are delayed by several days – and the container is left to stand in the direct sunlight. As the delay continues, the temperature inside the container continues to rise – until it finally reaches a critical range.
Or another example: a shock-sensitive component made of carbon fiber is to be transported to a plant in Mexico by truck. But there’s a construction site on the freeway so the truck can’t take the regular route. Instead the driver has to take a dirt track with potholes, causing a lot of vibration.
A condition monitoring system operating via sensor cloud allows exactly these potential quality defects in components and production materials to be tracked during transport. This significantly optimizes the procurement process. Firstly in the obvious sense that damaged material can be reordered in good time so as to avoid or at least minimize production loss. But it also makes it possible to negotiate with logistics service providers so they can take action to ensure this kind of problem doesn’t occur any more in the future.
“Houston, we have a problem”
But before everyone gets too excited about this new transparency, there’s one important thing to remember: most people are virtually drowning in information. And very few really need to have all the details all the time.
This is why SupplyOn only sends out exception-based warnings. In other words: only if the situation or schedule trend forecast is critical does the material planner receive an alert – whether in the app on a mobile device or via desktop. In a worst-case scenario, there are alternatives to choose from here so that early steps can be taken to prevent production stoppage.
And the Management Cockpit – where all location and condition data is analyzed – can be individually adapted to the information needs of specific decision-makers within the company. This means that people only get the information they really need. And if there’s no alert? Then they can either sit back and relax – or take care of other important business.
Different situation, same problem. Using the SupplyOn Mobile App to resolve an impending production material shortage: |