Increasing supply reliability and quality with Sensor Clouds
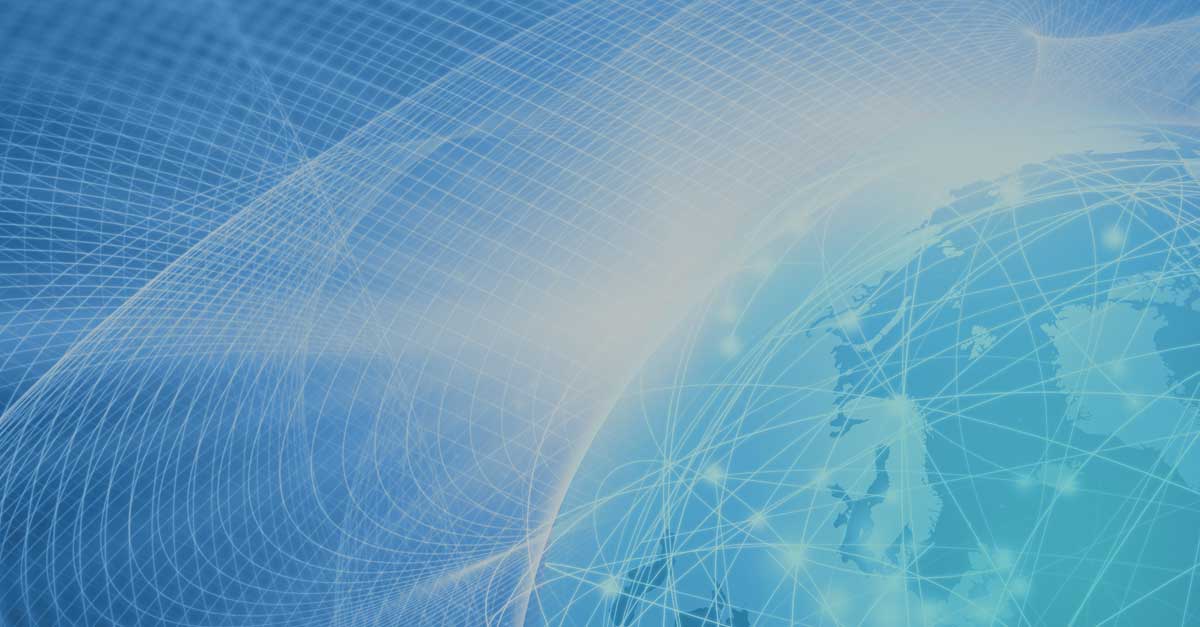
A leading aerospace supplier has further optimized its inbound supply chain with SupplyOn. As part of an innovative industry 4.0 project, sensor tracking was used to implement the real-time monitoring of deliveries. This not only aims at continuously determining location, but also the early detection of quality defects during transport due to excessive temperatures or moisture.
The challenge
The aerospace supply chain is highly synchronized, the components are sensitive and production times long. Any delays or damages in the transport of individual components have far-reaching consequences for not only the participants, but also for all subsequent stages in the supply chain. A leading aerospace supplier sought a solution that would provide maximum transparency of its inbound supply chain.
At the core were two questions: Will the ordered components arrive on time? And will they arrive undamaged? Since the company already uses the industry solution AirSupply from SupplyOn, it made sense to also implement it for such analyses.
In the initial step, SupplyOn analyzed the existing demand and incoming goods processes. It turned out, that the demand processes were already comprehensively covered by AirSupply. The challenge thus lay in the incoming goods process. How can supply chain disruptions be efficiently detected? How can material damages be detected early? How can the goods-receipt process be optimized to ensure stable production at maximum capacity?
The solution: Sensor clouds
SupplyOn’s Visibility & Analytics provides the answers to all of these questions. Therefore, AirSupply was to be supplemented with the respective Visibility & Analytics functionalities as part of an Industry 4.0 initiative. A particularly innovative and agile project approach was used, within only 90 days, the new solution was developed and piloted.
During the piloting process, particularly sensitive components were initially identified which were regularly exposed to problems such as temperature fluctuations or humidity during transport. For these components, the AirSupply function for coupling material with a container and a sensor (known as pairing) was used. When shipping, for instance, five packages of ten components each, the supplier can now consolidate these into one unit and scan the associated sensor number.
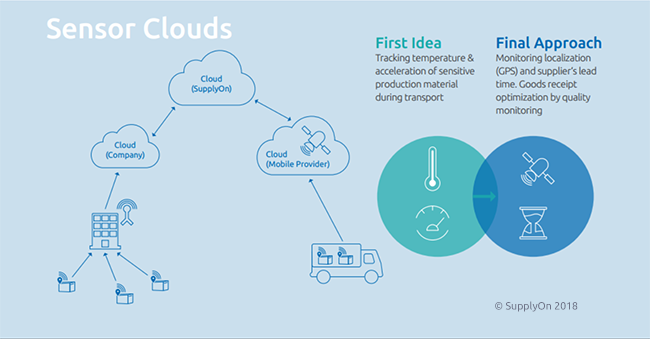
The supplier then only needs to enter the number of the sensor when generating the delivery note. For the supplier, all other processes remain unchanged. This was essential towards ensuring the highest possible acceptance level on the supplier side. From this moment on, the components can be monitored throughout the entire transport. The sensor continuously transmits position, temperature, and humidity in real-time.
Temperature monitoring played an especially important role for adhesives, whereas moisture analysis was used for metal parts. Position tracking of parts thus serves two goals: on the one hand, to monitor lead times and, on the other, to enable automatic decoupling of the sensor from the goods upon goods receipt.
The solution automatically tests whether orders and transports have been carried out within the agreed delivery time. This includes, for example, an evaluation of how many days remain until arrival at the plant and whether the lead time has been exceeded. The material planner thus has a precise overview of the current status of the delivery and can adjust the production processes accordingly. All position and status data are saved and can be used for reporting and analysis purposes.
The pilot was deemed a success after 90 days of testing and went into productive use.
The benefits
- Real-time monitoring of transport of critical parts with regard to delays in delivery and quality issues
- Determination of optimal transport routes with regard to delivery times and external influencing factors
- Improved supply reliability and delivery quality
- Stable production at maximum capacity through optimized incoming goods process
- High supplier acceptance thanks to simple integration into the existing order process
The video
SupplyOn will be presenting this and other innovative IoT use cases in a live demo at the Bosch Connected World 2018 in February. We would be happy to arrange an appointment with you.