There is no future without integrated production and logistics networks
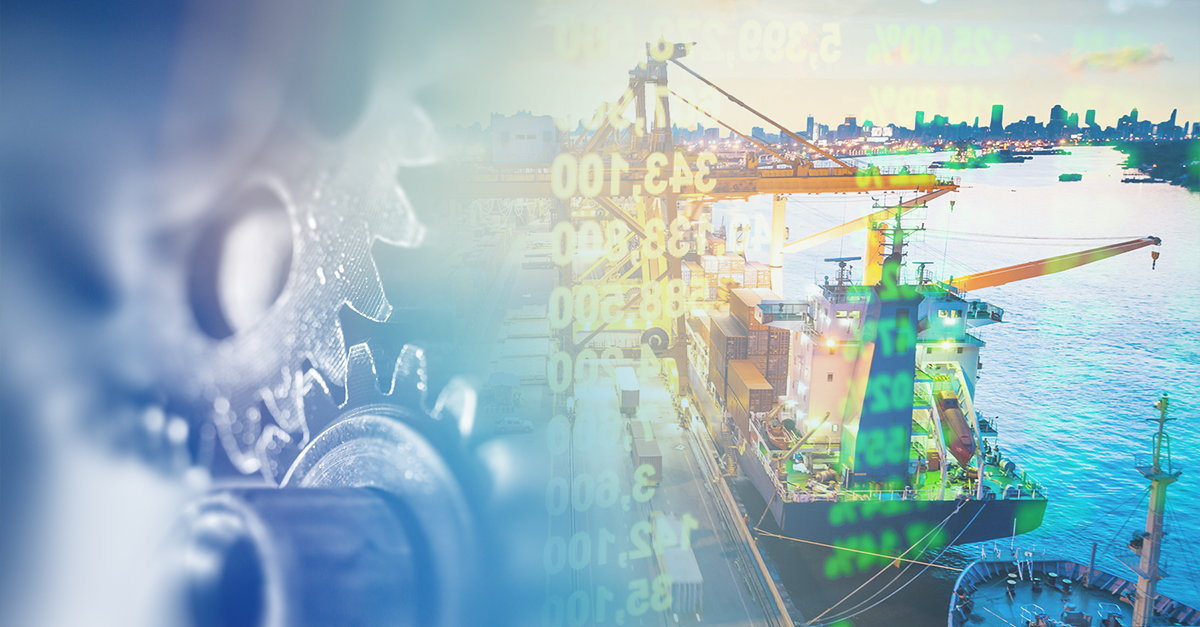
Much has already been written about flexible production and logistics networks, especially in economically turbulent times. However, the reality in many companies is still that production program planning and logistics planning run side by side in a non-integrated manner. Supplier integration, too, is usually only partially implemented.
An integrated approach is essential for a resilient supply chain
Yet an integrated approach and mutual optimization of logistics and production provide the basis for considering and cushioning uncertainties and disturbances in time. To do this, data needs to come downstream from planning via logistics to the supplier and upstream from the supplier to the customer. Specifically, this means, for example, providing the supplier with a demand forecast for the short, medium, and long-term horizon and, the other way around, providing the customer with the supplier’s capacity forecast.
Smart Factory: Lots of “beginners”, few “pioneers”
However, the industry is still a long way from this. According to a recent study by Cap Gemini, 72 percent of automotive companies are considered “beginners” in the implementation of the Smart Factory and only 10 percent are “pioneers” and thus equipped to exploit the full potential of intelligent factories (18 percent of OEMs are among the pioneers, compared to 8 percent of suppliers).
Actual demand is insufficiently accounted for
In most cases there is no planning and management of pick-up times, tailored to the actual daily requirements. Likewise, this also applies to the network’s dimensioning and buffer capacities. Worse, it is not designed for the materials, parts and components that are actually required. The routine re-adjustment that then follows is complicated, time-consuming and expensive. It is based on the domain know-how of program planners and dispatchers, who often cannot find the optimal solution because they lack the necessary data. They usually only see the data from their own plant. Cross-company data on stocks, delivery times, second source suppliers etc. are not available. The focus is always on solving the current problem at any price in order to prevent production interruption.
Collaborative partnership between customer and supplier is the key to success
But we have known for years that reliable and integrated production and supply networks will determine the competitiveness and continued existence of a company in the future. In order to achieve this, we need to adjust the way we deal with each other. Only collaboration based on a spirit of partnership and trust between customer and supplier guarantees long-term success. As a result of this, the customer will report his actual requirements and the supplier will not be penalized if he reports differently.
It’s about right-time, not real-time
A modern solution must support the design, configuration and continuous adaptation of material supply and order planning. With its Production-to-Supply solution, SupplyOn is pursuing precisely this goal and is replacing the real-time approach, which is still widely used today, with a right-time approach: Data from the supply network does not have to be constantly up-to-date, but only at the time of re-planning. But then, it must be as precise and correct as possible. This level of transparency then helps to establish an optimization logic that optimally combines the opposing goals of production program planning and logistics planning.
Substantial benefits by using artificial intelligence
SupplyOn is currently working on a cognitive enhancement of its Production-to-Supply solution, making it possible to evaluate disruptions and automatically suggest measures to eliminate these. Since the system is not only based on an employee’s domain knowledge but on company-wide knowledge, it is able to detect disruptions at an earlier stage and make suggestions for an optimum solution. The objectives are to reduce manual effort by two thirds compared to the current status, to avoid critical situations and to reduce costs for special shipments and replacement solutions by 50 percent.
All of this becomes possible through the trustful collaboration between supplier and customer: i.e. provision of reliable planning data by the customer and delivery of capacity, production and quality data by the supplier.