Automated goods receipt – part 1: Recording deliveries
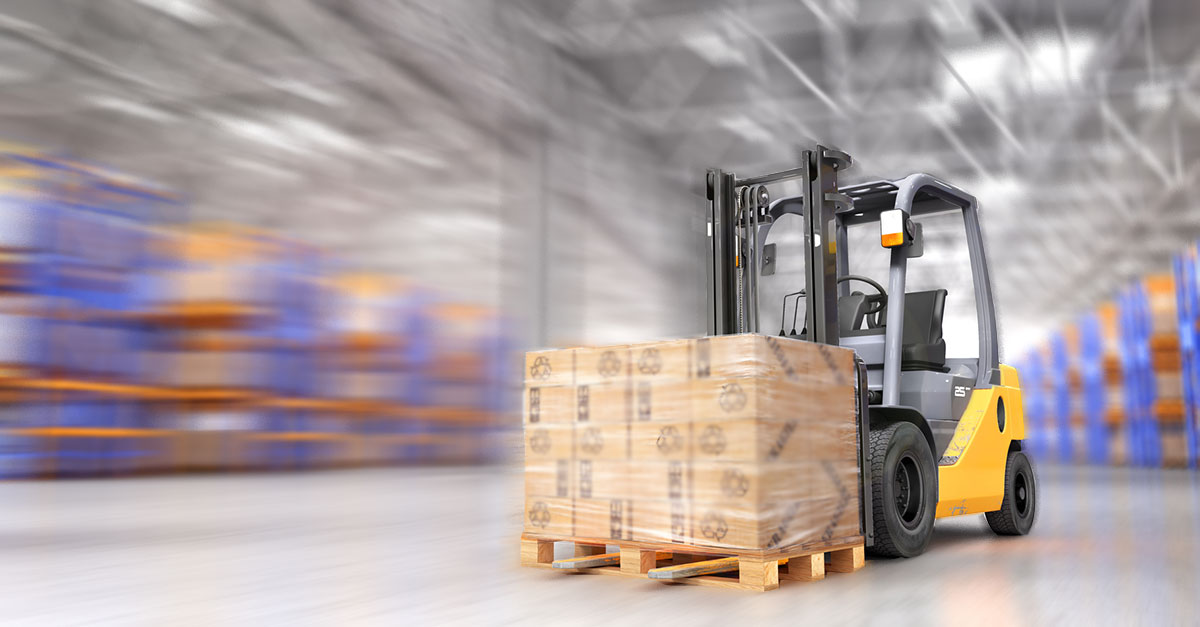
The electronic ordering process had just been successfully introduced. As I walk through my customer’s plant grounds after our final meeting, I think to myself “there sure are a lot of trucks in front of the gates,” and get into my car.
As soon as I get on the highway, I call my customer once more, “Mr. XXX, let’s talk about electronic delivery notification and automatic goods logging….”
In the subsequent discussion, it turned out that my customers are like many other manufacturing companies.
The employees are either very busy with an unexpected large amount of goods receipt or have nothing to do because there is no transparency with regard to the goods flow. Delivery trucks often end up waiting and are unloaded slowly. Thus, surcharges for waiting periods on the transport cost calculation are not uncommon.
The stock levels of many materials are too high, since no one knows exactly when that supplier will deliver again. It’s better to have too much security stock than too little, which again unfortunately ties up a lot of capital.
Entering paper documents manually into the ERP system during deliveries takes a lot of time. Printing labels which must be applied to the delivered goods for subsequent production and logistics processes is just another necessary resource-consuming evil.
Have you recognized yourself in some of these aspects? Then I’d like to invite you to read this article. It is about exactly these challenges and answers the following questions:
- How do I ideally plan my goods receipt resources?
- How do I avoid lengthy and cost-intensive waiting periods of freight forwarders?
- How can I reduce the capital tied up in security stock?
- How do I eliminate and reduce the manual and error-prone goods receipt processes?
- How can I avoid cost-intensive relabeling?
I will provide the answer to these questions beforehand: by switching your goods receipt to automated and electronic processes!
In the following article, I’ll explain, from practical experience, how this works and what you need to bear in mind.
Electronic ASN Notification as a Basis (ASN Process)
An essential component is the electronic goods delivery notification by the supplier, which is usually done with an “ASN” (Advance Shipping Notice). The supplier records some basic data in advance, which is then transmitted electronically at the departure of the freight forwarder and forms the basis for the efficient receipt of goods.
Important information:
- Supplier’s delivery note data, such as delivery note number and delivery item
- Planned delivery date (calculated automatically based on predefined lead times)
- Material data, including material number, name and quantity, batch and country of origin, if available
- Order numbers or master contract numbers
- Packing information for transport containers or pallets
The data can be recorded either in the supplier’s ERP system or on an online platform. If the supplier uses their own ERP, data must be transferred to the customer system via the EDI interface. However, this assumes that the customer has set up such a EDI connection with all their suppliers. Experience has shown that this is rarely the case. In most cases, a large part of the document and order volume can be exchanged by EDI. A complete solution remains a nice fantasy, however.
With a web-based communication platform such as the SupplyOn Purchase-to-Pay solution, suppliers with EDI interfaces as well as small, less technologically established suppliers can be integrated. This should result in nearly 100% coverage of the process.
By using such a platform, sophisticated reports on supplier quality can be generated. A comprehensive alert system is used in case of deviations. It informs the supplier and the customer’s material planner automatically about overdue deliveries, for example. Time-consuming, manual and permanent monitoring of the supply chain is therefore unnecessary. The employee must intervene only in the event of a deviation.
Improved capacity planning through higher transparency
But back to the notification process. The information entered by the supplier on the shipping notification is now stored as structured data in your ERP system. An inbound delivery is also generated. Based on this data, you get information about which goods are en route a few days or even weeks in advance. This enables you to set up a clear and more accurate goods receipt capacity planning.
You now also know that material which could possibly create a bottleneck is on its way. Your employees can include this information in their material and production planning. This allows you to systematically reduce capital-intensive security stocks. Moreover, the planning effort for your employees is considerably reduced as many manual inquiries and coordination with the suppliers become unnecessary.
Because the capacity in goods receipt is much closer to the actual requirements, waiting times for the unloading of incoming trucks are reduced. Your goods receipt employees are thus fully utilized with regard to additional work and idle times.
Reduction of manual work in the goods receipt
Probably the biggest gain you achieve from an automatic goods receipt system is the reduction of manual activities. Whereas you currently have to transfer all deliveries from paper delivery notes into the system as a manual, error-prone process, all relevant data are already available if the goods are logged electronically. To log the goods, the employee only has to identify the applicable data record in the system based on a reference (i.e. order, supplier and delivery note numbers). They can then log it at the push of a button. All relevant information is already entered in your system.
“Beep” and done – automatic recording with a scanner
During the notification process, the supplier has already printed documents such as the delivery note or transport order. These are attached to the goods. Goods labels are attached to the packs and handling units, such as a pallet or a lattice box. The labels can contain a wide range of information on the material or supplier. Important information is usually printed in the form of a (2D) barcode.
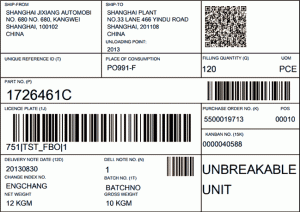
There are some standard labels, such as VDA 4902 (particularly common in the European manufacturing industry), ODETTE, or the relatively modern GTL V3 label. The latter is becoming more and more prevalent as a global standard.
Sometimes though, the standard labels may not meet the customer’s requirements. For example, because of their size, they are not suitable for small load carriers or the information on the labels is not sufficient. A customer-specific label can then be used.
Now however, the supplier must also be able to print this label. Standard labels are generally feasible. But programming of customized label poses technical and procedural problems for most suppliers. The use of a standard platform such as SupplyOn which automatically provides all relevant documents for the supplier will come in very handy here.
Equip your goods receipt with a scanner and all incoming deliveries can be identified and logged automatically by scanning. This reduces the workload considerably. By the way, automatic logging can also be combined with scenarios such as RFID tags or Bluetooth transmitters, which identify the data record instead of scanning the label.
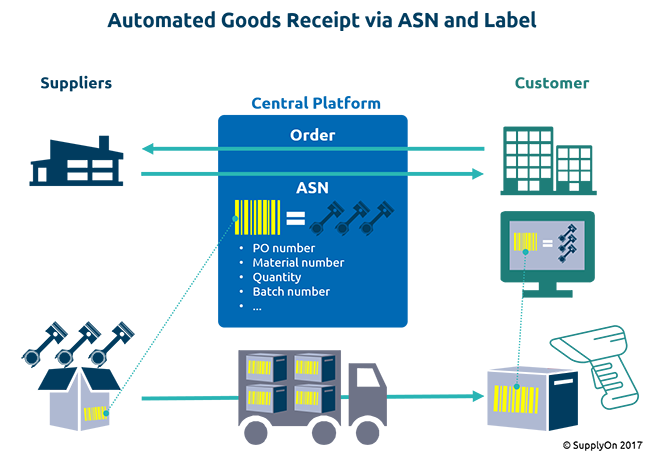
This worked perfectly for my customer. The scanners are diligently beeping as they perform their job and the workload has decreased significantly. To find out how we abolished the time-consuming process of relabeling, please see part 2 of my article.
I hope I have been able to give you some food for thought. I look forward to your comments concerning your experiences and challenges!
Yours, Florian Boehm