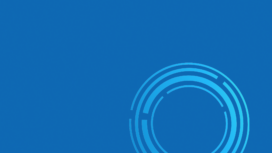
Satisfied Customers
Vendor Managed Inventory at Robert Bosch North America
Vendor Managed Inventory (VMI) strengthens the relationship between customer and supplier allowing for the flow of material and information to occur seamlessly. Instead of responding to phone calls, e-mails, and guess-work, the integration of SupplyOn VMI and the customer’s backend systems allows for real-time communications based on actual requirements.
SupplyOn VMI and integrated supply chain technologies allows the customer to communicate delivery schedules, actual stock-on-hand quantities, and goods receipt information. SupplyOn VMI provides the customer multiple material flow solutions based upon a ‘plan for every part’ concept. Not every part in a manufacturing process is planned, transported, and consumed equally. SupplyOn developed VMI in conjunction with WebEDI to support the multitude of material flow solutions required in a supply chain relationship.
Robert Bosch North America’s (RBNA) automotive division is a leading Tier 1 supplier providing finished goods material to all OEM’s in North America, Europe, and Asia. To support the global reach and varied OE plant production schedules, in 2003 RBNA started the implementation of SupplyOn VMI and WebEDI to all North American manufacturing facilities encompassing 100 percent of their commodities, parts, and suppliers.
One major objective at RBNA Automotive is for production suppliers to ‘Replenish based on Consumption’ allowing the leveling of customer orders over time. To accomplish this task, key Bosch North American locations have moved from weekly to daily shipments requesting suppliers to ship smaller lot sizes. The daily production schedule takes into account finished good requirements, transit times, and supplier manufacturing capabilities. To manage the Bosch Production System (BPS) process, suppliers must maintain 1-3 days of finished goods at their location in order to support a smoother replenishment signal based on consumption of material.
This case study examines the implementation of VMI/WebEDI at the Charleston plant in North Carolina. The Charleston plant is the largest in North America with timely and complex manufacturing processes. The plant manages over 2000 production parts with 175 suppliers domestically (60%) and internationally (40%). Charleston manufactures Fuel injectors for diesel and gasoline-powered engines, and Antilock Braking System (ABS) brake components utilized mostly in North America and Europe.
The Charleston plant each day updates SupplyOn Vendor Managed Inventory with new stock-on-hand quantities in the calculation of new part shipment quantities based on min/max levels and what is in-transit. Suppliers to Charleston access SupplyOn VMI on a daily basis to determine their next shipment quantity. Advance Shipping Notifications (ASNs) created online or through traditional EDI, provide the visibility required for the plant to manage in-transit material. Planners can track late or missed shipments or manage part critical shortages based on consumption and future demand.
The VMI module can be configured to simulate a Pull Signal based on consumption. The Charleston supplier ships material in a just-in-time environment, coordinating requests from the plant and logistics carrier. The ability to move from weekly to daily shipments has reduced inventory levels to the point where no outside warehousing is required. Material is shipped directly to the manufacturing line in smaller container sizes, matching shipments with the daily production schedule. The inbound material receiving process at Charleston is streamlined allowing the dock to receipt all material with one keystroke, reducing errors, and allowing the ERS payment process to the supplier to occur efficiently.
Bosch also uses SupplyOn VMI to measure a supplier’s delivery performance. Staying within system generated inventory levels, as well as shipping the correct quantity when required, allows to measure the accuracy and timeliness of the shipment. Bosch uses this data to ensure key inventory levels are met, track under and over shipments, as well as how the supplier interacts overall with Bosch´s BPS ‘Replenish based on Consumption’ requirement. As an additional benefit to the Bosch material flow process, the Charleston plant interacts with their third party logistics provider (Transfreight) for designing and supporting milk-run and full truck load deliveries to the North American plants. Each work day SupplyOn VMI communicates shipment and packaging information to Transfreight for the improvement of ‘cubing of trailers’ and ‘optimizing pickup schedules’.
Over the years the Charleston suppliers have also benefited from Bosch´s VMI implementation. Suppliers are able to view current stock-on-hand levels, quickly determine correct shipment quantities, track ASNs and Goods Receipts, and monitor their delivery performance. SupplyOn Vendor Managed Inventory also allows the supplier’s planning, manufacturing, and inventory levels to improve as well. In a 2005 Charleston study, VMI suppliers were more likely to reduce their inventory levels and improve material planning requirements with their suppliers than those that did not.
‘One key benefit of VMI for Charleston is its ability to communicate a daily ship schedule and pull signal matching OE requirements with the plants’ production schedule”, noted Nayak Ullal, Project Manager for SupplyOn at Charleston. It is very easy for the material planner to set inventory levels and have the VMI module inform the supplier of their next shipment quantity. ‘SupplyOn VMI has allowed Charleston to reduce daily inventory levels by 30 percent, premium freight by over 70 percent, and ensure the delivery performance of our suppliers is at the highest levels’ commented Ullal. With the added capabilities of SupplyOn VMI the planner can track inbound material, receipt material at the dock quicker, and monitor line shut downs and critical shortages online.
With the success achieved at the Charleston plant, Bosch has rolled out SupplyOn VMI to all their North American plants. The benefits to inventory control, transportation costs, and material flow enhancements are now achieved through all North American and International part movements. Robert Bosch North America is now able to manage centrally through SupplyOn common objectives and cost reductions that could not have occurred before. Using SupplyOn as central supplier portal elevates the Bosch organization in its automotive and other key industries as a leader in supply chain management business process solutions.
More case studies on Vendor Managed Inventory
You would like to get more information on Supply Chain Collaboration?
Just enter your contact details and we will get in touch with you as soon as possible.