How to implement an efficient risk management system
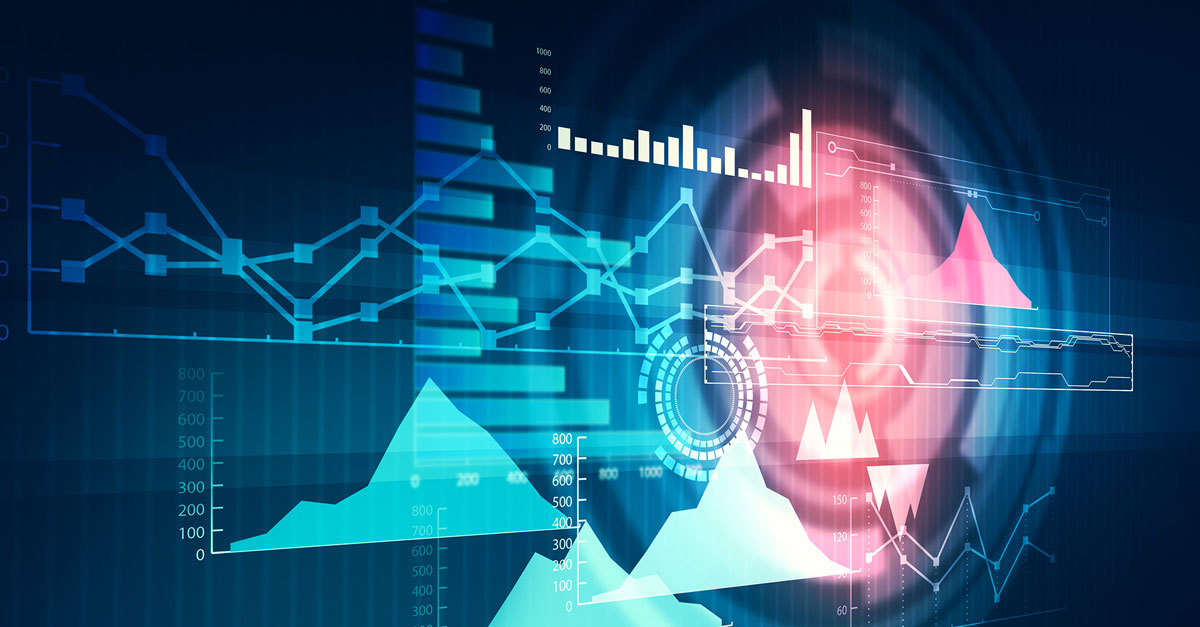
The coronavirus pandemic has posed enormous, unprecedented challenges for companies. Efficient risk management plays a central role in meeting these challenges. It is not so much a question of whether the current situation could have been anticipated and planned for. Rather, the focus is on how companies can now best protect their core processes and increase the resilience of their operations.
The important thing here is not only to look at the current situation. Namely, how you can maintain production in the face of acute supply chain bottlenecks and which materials at which locations are particularly affected. Just as important is a look into the near future: Where do potential risks lie if production picks up again? How can you manage supplier capacities or help suppliers with planning when you yourself only have uncertain sales forecasts? As global supply chains are about to restart now, how can you implement a suitable early warning system alerting you of possible delays, especially at the bottleneck of (sea) transport? How can you also identify and monitor the effects of external events, be they major or minor, on your own supply chain as early and as accurately as possible? And finally: which countermeasures can you take, which ones are the most efficient?
It all starts with data
All this requires relevant data. In times of electronic processes, digital supply chains and digital twins, it’s not so much the pure amount of data that is the problem. Rather, it is the efficient use of this data that is crucial. After all, this is the key to drawing the right conclusions about the reliability of your own supply chain.
But knowledge only comes from combining data
However, this efficient use of data often fails because they are stored in separate data silos and are difficult to merge. Yet: without data consolidation, there are no meaningful results for risk assessment. The best analysis tools are worth little if they are not fed with all the relevant information available.
This is precisely the problem with most risk management tools used in many companies to date. These are often implemented as a stand-alone solution, decoupled from the underlying business processes and thus also from the supply chain. However, you can only properly assess and mitigate a potential risk when you know how an event specifically affects your supply chain, and thus the flow of materials. In other words, this is about questions such as: Which supplier exactly is affected? Which specific transport is impacted? Which materials are affected? Precisely how severely does it impact the flow of my materials? And, as result, how does this affect my production in specific plants?
Holistic risk management approach needed
Only with such detailed knowledge you can then initiate the appropriate countermeasures. But this requires a holistic approach. This approach has an equal focus on suppliers, processes and external events.
Suppliers: detecting delivery issues early on
In the case of the suppliers, this concerns issues such as their own reliability with regard to product quality, punctuality of delivery and agreed delivery quantities (OTIF: on time and in full). Another issue is the economic stability of the suppliers, i.e. their risk of insolvency. Furthermore, supplier capacities remain a key topic: In boom times, it is all about managing scarce capacities. In times of crisis, it is about reliable forecasts of capacities that are actually available.
In this context, it is essential to look at the various stages of the supply chain, catchword: n-tier reliability. It is the question of how reliably my supplier’s suppliers can fulfill their delivery promises.
This is precisely where multi-tier supply chain networks such as SupplyOn excel, bringing together three or more stages of a supply chain on a digital platform. For instance, customers using the Production-to-Supply solution can directly look into their suppliers’ production processes and thus learn about potential delivery bottlenecks at a much earlier stage, e.g. when supplies of critical materials to their suppliers are stalling.
As a preventive measure, businesses can also use surveys to obtain details on ISO standard 22301 and the Business Continuity Management (BCM) concepts from their suppliers. These surveys service not just as a preventative tool. They also help you during in-crisis management to better understand the specific challenges your supply chain is facing. To this end, SupplyOn offers its customers ready-to-use questionnaires. Companies can further adapt these to their specific needs or send them directly to their entire supplier base with just one click. The answers can then be evaluated automatically via SupplyOn.
Logistics: minimizing process risks
Next to the situation at the supplier, it is equally important to keep track of the logistics processes. This involves a number of topics, ranging from smooth electronic collaboration with the supplier, through immediate detection of possible transport damages, to early warnings about transport delays (see also: 3 uses cases how companies benefit from Smart Logistics Data).
External events: Identifying disruptions in the delivery network
Even if suppliers, carriers, forwarders and businesses have their processes optimally under control, these processes can still be disrupted by external events. These events can be anything from weather extremes and natural disasters to trade or political disputes, strikes and even the current pandemic.
To obtain early warning of possible disruptions to the supply network, you can draw on a wide range of data sources. Nonetheless, in terms of data consolidation, it is vital to efficiently combine this data from the various sources and to match it with your own supply chain network.
Integrated Supply Chain Risk Management combines SCM processes with risk data
For this purpose, SupplyOn connects all data sources via standardized interfaces in a way that enables a consolidated and hence highly insightful analysis. We achieve this by enriching the data from the operational ordering process, such as article numbers, transport routes and discharge points, with data from external data sources. This data includes information on weather extremes and natural disasters as well as information on traffic jams and strikes.
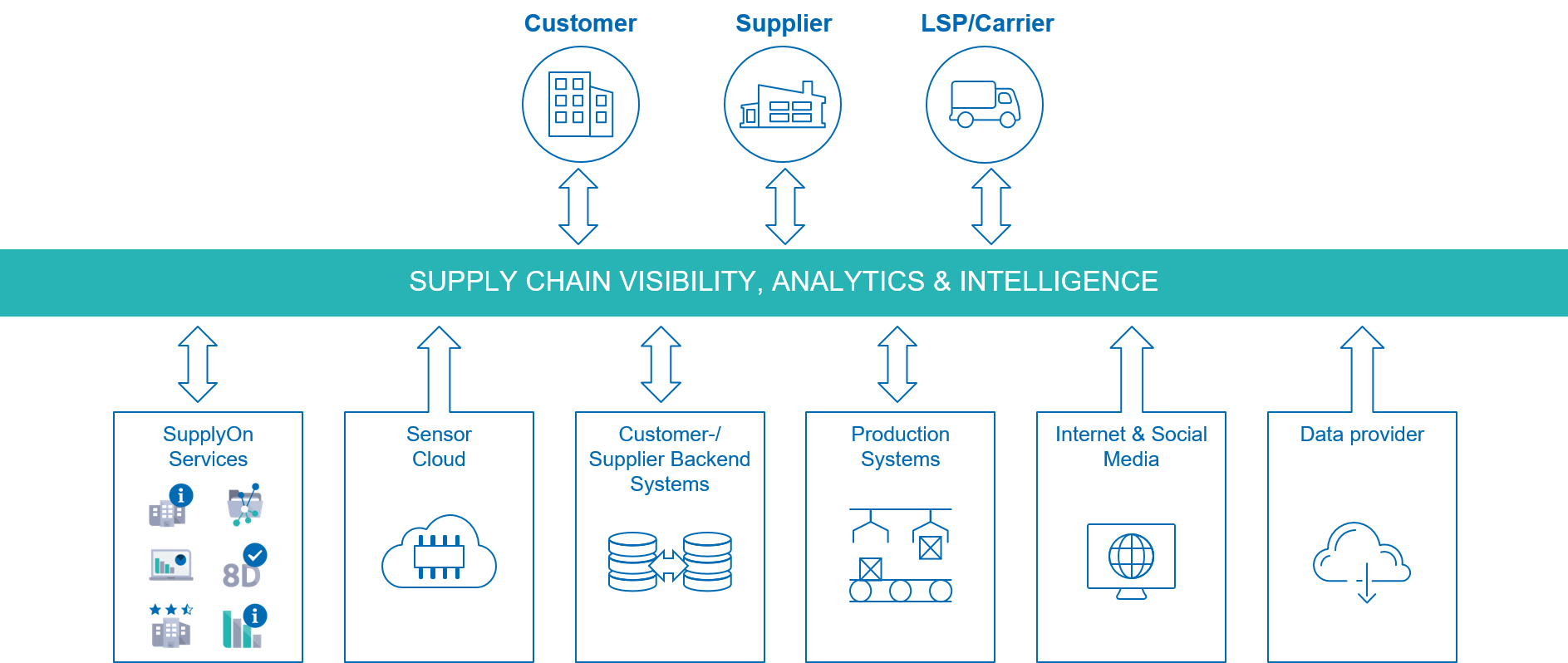
The analyses can even integrate highly unstructured data from social media such as Facebook and Twitter. On top of this comes data from sensors that continuously monitor environmental conditions such as temperature and humidity during the transport of sensitive components.
In the event of a problem, these data provide a comprehensive picture. Disposition staff learn at an early stage whether there is a problem with a particular transport. Plus, they can also precisely identify which purchased part and thus which production step on their side is affected. With this information, they can now take targeted action, depending on how important the affected part is for their own production or for the customer. This helps you to control precisely the effort and thus the costs of solving the problem.
Visibility along the supply chain
Fully in line with the concept of a holistic solution, SupplyOn Analytics offers companies the option of processing this data in their own systems. In addition, they can also make the analyses available to third parties, such as customers. All this can help to increase transparency along the supply chain.
Implementing risk management step by step in the supply chain
Even though the current situation calls for immediate action, risk management is a strategic issue above all. Of course, you can quickly and easily implement single measures in an acute crisis. However, in order to derive the greatest long-term benefit, companies should not implement risk management as an off-the-shelf, stand-alone tool. Most importantly though, a step-by-step approach to risk management has proven its worth.
The first step is to improve the collaboration with your suppliers, thereby eliminating process risks through improved visibility. In the second step, integrating external data sources helps to increase visibility further and enables you to better respond to external events, for example. And third, as the most sophisticated discipline, in-crisis risk management serves to optimally manage sudden, unforeseen risks at the operational level.