What’s new at SupplyOn? The results of the last Program Increment (PI)
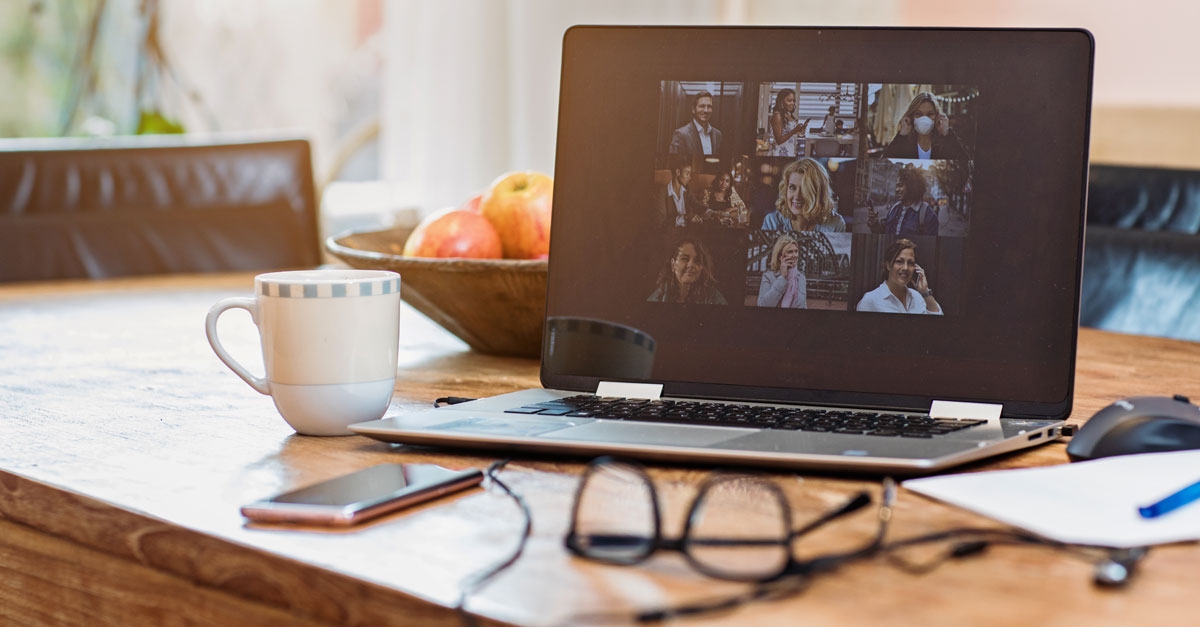
Agile software development not only involves planning for the future, but also always looking back: What (and how) did the various development teams do over the last twelve weeks? What innovations and improvements are there in the individual areas? And: Which planned steps from the previous PI Planning could be implemented … and how?
All these questions were answered in detail by the respective product managers in the latest PI System Demo.
Presentation of the new developments—bringing everyone on the same page
The PI System Demo is mainly intended for internal knowledge transfer. During the development phase (so-called Program Increment = PI) the individual teams are focused on their respective topics and projects. As a result, they are usually less aware of what is happening in the other teams. It is therefore important to regain an overview of the whole, to be inspired by the solutions of colleagues and to learn from each other. This can also provide possible starting points for future solutions.
But the PI System Demo is not only productive for our development teams. Especially our sales and consulting colleagues benefit from the presentation of the latest software developments. These in-depth insights into all new developments help them in turn to keep our customers up to date, to offer them competent advice and to ensure that they benefit as much as possible from the further developments.
The innovations in PI 2020-2
But what exactly are these further developments? Here is a small excerpt:
Supplier Management
Several improvements were introduced in Supplier Management: For example, the invitation strategy for the flexible surveys was refined. This ensures that there are no duplicate invitations when uploading invitation lists or selecting recipients directly in the Survey module. In addition, existing users in the invitation lists can be identified and invited with the appropriate role. The evaluation options have also been further extended. The reports now also contain information on the exact delivery status and on forwards to colleagues.
A further key aspect is the master data quality. For this, it is now possible to define a maximum certificate validity date and validate the entries accordingly.
Source-to-APQP
A new function has been added to the auction solution: SupplyOn customers can now benefit from a flexible bundling option for items in a multi-lot auction. The buyer creates suitable article packages and assigns them to the appropriate suppliers. Each of these bundles is allocated individually. In this way, the buyer always obtains the best offer for the entire package and thus saves a great deal of manual comparison and negotiation effort.
Procurement
The range of functions in the Central Procurement Hub has also been expanded. Numerous enhancements ensure that the connection of catalogs is even more seamless and smooth. This eliminates manual effort on both the customer and supplier side.
Invoicing
With the PDF solution, customers benefit from simpler and more transparent processes with suppliers who use their own solutions (e.g. ERP system) for invoice generation. Suppliers can simply send PDFs to SupplyOn by e-mail instead of entering the data via the web interface. The customer benefits from fully validated and structured data, while the supplier can continue to use his proven way of invoicing without having to implement a fully automated interface such as EDIFACT.
Supply Chain Collaboration
The new module “Paperless Goods Receipt” is an essential component for companies in the implementation of paperless goods receipt. The extension ensures that all documents required for further processing of the goods (e.g. certificates, sample releases, test reports, manuals, pro forma invoices, etc.) are already available in electronic form before the goods arrive and are made available for further processing via the newly developed document interface. The integrated alert management monitors the document provision. This reduces manual activities in incoming goods, eliminates sources of error and significantly reduces process delays. In addition, the documents can be fully automatically linked to quality, customs and transport processes and archived in the internal DMS with all necessary keywords.
Quality Management
Various SupplyOn Quality Services have been expanded: Technical Review was supplemented with additional functionalities. In Project Management, customers can now link projects with each other and thus gain a better overview of the current status and progress of all related projects. It is also possible to create a master template to cover several material categories. In Action Management, new columns can be configured to map the findings and root causes for an audit.
Visibility – Analytics – Intelligence
In close cooperation with the UI/UX team, six new usage monitors were implemented, among others for Sourcing and SCM. However, a special focus was placed on the Production-to-Supply Suite. In the area of capacity management, new dashboards ensure better handling of capacity risks on both the customer and supplier side. An overall view (not only plant-specific) provides a complete overview of bottlenecks for an entire parts family.
The Transport Volume Forecast provides companies with an overview of what transport volumes the carriers can expect per location in the near future. This helps the carriers to plan their networks—and the companies gain certainty about when the material will arrive at their plant.
Transport Management
The solution for dock slot management was developed together with EURO-LOG. It enables users to configure loading and unloading points. Freight forwarders can book the ramps created there. This helps to organize and process the incoming and outgoing transports of a logistics center. With the access to the collaboration platform, the users are provided with a tool that guarantees a smooth and efficient transport execution.
On to new developments: Full speed ahead
Great to see what the individual teams have accomplished in the twelve weeks. But there is no time to rest on one’s achievements, as there’s always the next PI coming up.
So, stay tuned!